VEOLIA Water optimises green hydrogen production
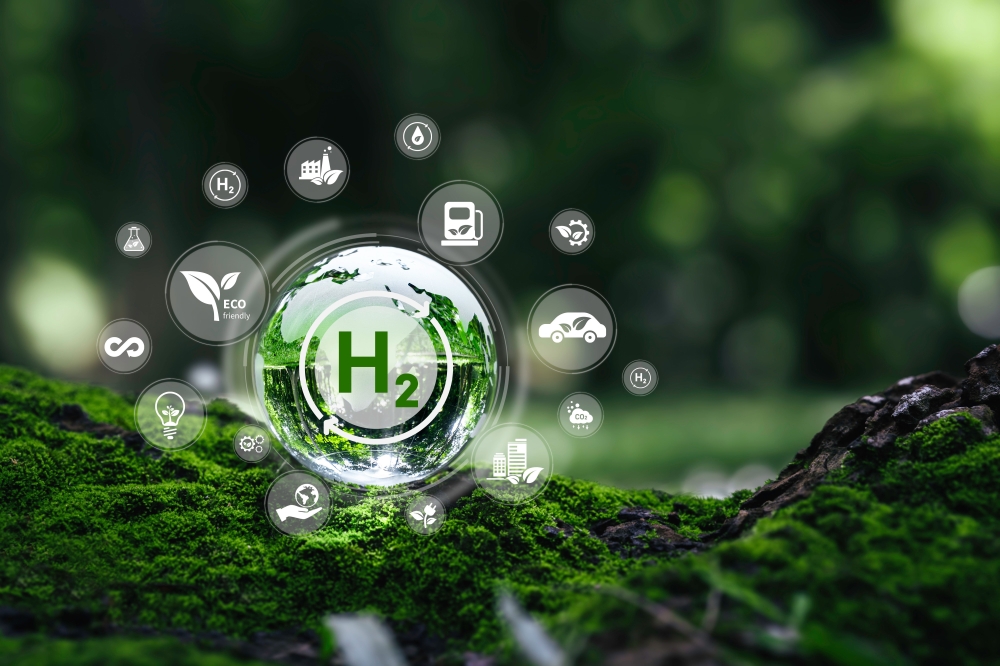
Veolia Water Technologies has partnered with a major producer of green hydrogen and helped the company to increase production, whilst also reducing the volume of wastewater put to drain. Veolia Water Technologies supplied its TERION™ S 4000 unit, which combines reverse osmosis (RO) and continuous electrodeionisation (CEDI). This chemical-free solution enables the continuous supply of pure water and reduces the likelihood of the electrolysers sustaining damage by running dry.
The customer is a manufacturer of Proton Exchange Membrane (PEM) electrolysers and a leading producer of green hydrogen – a key fuel in global progress towards net zero. Having developed a tried-and-tested method, it was seeking to expand its production. As water is crucial for electrolysis – the process by which green hydrogen is generated – the facility required an increased volume; specifically, a constant stream of 4000 ltr/rh of water with a conductivity of <0.1µs/cm.
However, the customer’s previous water treatment plant had relied on standard units with exchange cylinders. Due to the low conductivity levels needed for the feed water, the polishing cylinders were exhausting quickly, resulting in expenditure for their regeneration and costly downtime. In addition, the existing RO plant used 40 litres of water for every 20 litres of pure water produced for electrolysis, so a lot of water was being rejected and put to drain, which was at odds with the company’s sustainability goals. As such, the customer sought a new water treatment system that would not rely on chemicals at any stage of the purification process to avoid degradation of the electrolysers.
Veolia Water Technologies proposed its TERION™ S 4000 unit, which combines RO and CEDI processes to ensure a chemical-free supply of pure water. Having worked with other hydrogen producers, Veolia Water Technologies were able to offer experience with this kind of system delivery and recommend the creation of a central ring main system for the entire facility, which would utilise the single TERION™ S 4000.
The proposal also included 50,000 litres of water being held in storage to ensure the electrolysers would continue running, even if an unscheduled outage should occur. This aspect was crucial for the customer as the electrolysers can sustain damage if they run dry.
The TERION™ S 4000 combines RO and CEDI into a single package. RO is highly effective at removing up to 99% of dissolved solids using a semi-permeable membrane that captures contaminants from the pressurised feedwater. CEDI is implemented after this to provide water polishing. This uses electricity combined with an ion exchange membrane to remove ions from the water. Unlike standard ion exchange, and the customer’s previous system, the resin beds are constantly regenerated by the electric current. Consequently, no downtime is required, resulting in a constant supply of water and saving the customer both money and hassle.
The highly efficient TERION™ S units ensure that less water is wasted and put to drain. Combined with the customer’s use of renewable electricity, this element of the technology has helped to align the facility with the company’s overall sustainability goals.
Veolia Water Technologies integrated its Hubgrade digital monitoring system with the water treatment package. This accurately tracks the status of the water delivery system and quickly and easily picks up on issues or faults, reducing the likelihood of downtime.
Ben Moore, Business Development Manager at Veolia Water Technologies, commented, "We were thrilled to be able to offer the customer our expertise and previous experience with optimising hydrogen production. Not only have we been able to provide an efficient, chemical-free solution, but we have also been able to make it more sustainable – thanks to the high recovery rate of the TERION™ S.”